Installing Roof Deck
When you are thinking of commercial roof installation in San Gabriel, the roof deck is the first thing that you would need to install. The roof deck is the structural base of the roof, typically made of wood, metal, or concrete. It provides the foundation for the other roof components. Get in touch with Jake Roofing, to get the best solutions.
The Different Types of Roof Decks
Steel Deck
Steel roof decks are widely used in commercial buildings due to their strength, durability, and fire resistance. They consist of corrugated steel panels that provide structural support and serve as a base for roofing materials.
Concrete Deck
Concrete roof decks are suitable for larger commercial buildings where heavy loads need to be supported. They are typically constructed with reinforced concrete slabs that offer excellent strength and durability

Wood Deck
Wood roof decks are often used in low-rise commercial buildings or in combination with other materials. They are lightweight, cost-effective, and relatively easy to install. Common types of wood decks include plywood or oriented strand board (OSB) panels
Composite Deck
Composite roof decks combine different materials to optimize strength, durability, and performance. For example, a composite deck may consist of steel beams with a concrete topping or a combination of wood and concrete elements.
Structural Insulated Panels (SIPs)
SIPs are prefabricated panels made of rigid foam insulation sandwiched between two layers of structural sheathing, such as plywood or OSB. They offer excellent insulation properties and can be used as both roof deck and insulation
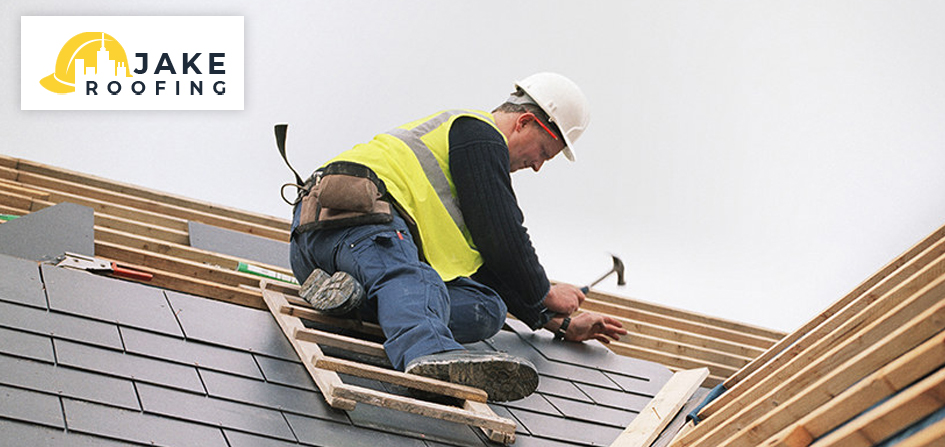
The Process of Installing Roof Deck
Material Selection
Based on the project requirements, the appropriate type of roof deck material is selected. This may include steel, concrete, wood, or composite materials.
Preparation
The roof surface is prepared by cleaning, removing any existing roofing materials, and ensuring it is smooth and free from debris. Necessary repairs or modifications to the existing roof structure are also made.
Installation of Roof Deck
The selected roof deck material is installed according to the manufacturer’s guidelines and industry best practices. This may involve securing the deck panels or elements, such as steel beams or joists, in the desired configuration
Waterproofing and Insulation
Depending on the design and building requirements, a waterproofing layer and insulation materials may be added to the roof deck. This helps protect the building from water infiltration and provides thermal insulation
Roofing System Installation
Once the roof deck is in place, the roofing system is installed on top of it. This may include additional layers such as underlayment, membranes, and the final roofing material, such as shingles, metal panels, or a single-ply membrane
Quality Assurance and Inspections
Throughout the installation process, quality assurance measures and inspections are conducted to ensure that the roof deck and roofing system meet the required standards and specifications.
Choosing the Right Membrane for Commercial Roof Installation in San Gabriel
Choosing the right roof membrane is a critical step for commercial roof installation in San Gabriel. The roofing membrane is the outermost layer of the roof, serving as the primary waterproofing barrier. It can be made of various materials such as single-ply membranes (e.g., EPDM, TPO, PVC) or built-up roofing (BUR) systems
Single-Ply Membranes
Single-ply roofing membranes are widely used for commercial roofing due to their durability, flexibility, and ease of installation. These membranes are typically made from synthetic materials, such as PVC (polyvinyl chloride) or TPO (thermoplastic olefin), and offer a seamless, watertight barrier for the roof.
The primary purpose of single-ply roofing membranes is to provide waterproofing and weatherproofing for commercial buildings. They are designed to withstand UV radiation, temperature extremes, and other environmental elements. Additionally, single-ply membranes are resistant to chemicals, punctures, and tears, making them suitable for a wide range of commercial applications.
Built Up Roofing
Built-up roofing (BUR) is a traditional and widely used method for commercial roofing. It consists of multiple layers of asphalt-impregnated felt, also known as roofing ply, alternated with layers of bitumen (asphalt) and finished with a layer of gravel or a reflective coating.
The process of installing a built-up roof typically involves several steps. First, a vapor barrier or insulation layer may be applied to the roof deck. Then, multiple layers of roofing ply are installed, with each layer being bonded together using hot bitumen or adhesive. The process is repeated to create a multi-layered, durable roof system. Finally, a top layer of gravel or a coating may be added to protect the roof from weathering and provide additional fire resistance.
Here’s a table comparing the factors to consider when choosing a roofing membrane for a commercial roof installation in San Gabriel and how single-ply roofing and built-up roofing (BUR) measure against each of them
Factors to Consider | Single-Ply Roofing | Built-Up Roofing (BUR) |
---|---|---|
Installation | Easier and faster | Labor-intensive and time-consuming |
Cost | Generally more expensive | Cost-effective in the long term |
Waterproofing | Excellent waterproofing capabilities | Offers effective waterproofing |
Durability | Resistant to UV rays and chemicals | Durable and long-lasting |
Maintenance | Minimal maintenance required | Regular maintenance and recoating |
Weight | Lightweight | Adds weight to the roof structure |
Compatibility | Compatible with different roof systems | Compatible with various substrates |
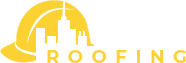
Frequently Asked Questions
Roof coatings can have a significant impact on commercial roofs. They are designed to provide an additional layer of protection, extend the lifespan of the roof, and enhance its performance. Here are some key impacts of roof coatings:
Enhanced Durability: Roof coatings create a protective barrier that shields the roof from UV rays, extreme temperatures, and weather elements, reducing the risk of damage and deterioration.
Energy Efficiency: Certain roof coatings have reflective properties, which can help reduce heat absorption and lower energy costs by keeping the building cooler.
Waterproofing: It also acts as a waterproofing layer, preventing water penetration and reducing the risk of leaks, moisture damage, and mold growth.
Extended Roof Lifespan: By providing an added layer of protection, roof coatings can help extend the lifespan of the roof, delaying the need for a costly roof replacement.
Cost Savings: You can get cost savings by reducing energy consumption, minimizing the need for repairs, and extending the roof’s lifespan.
The duration of the roof installation process can vary depending on various factors such as the size and complexity of the commercial building, the type of roofing system being installed, weather conditions, and the efficiency of the roofing contractor. It’s important to discuss this timeline with your contractor, as they will be able to provide a more accurate estimate based on your specific project.
In most cases, a commercial roof installation can take anywhere from a few days to a few weeks. This includes the time required for preparation, removal of the existing roof (if necessary), installation of the new roofing materials, and any additional work such as flashing, insulation, or membrane application
Depending on your location and the specific requirements of your local building authorities, permits may be required for certain types of roof installations or modifications. You will get all the necessary assistance to get the required permits from the San Gabriel municipal authorities.